It is a simple scientific fact that it takes less energy to accelerate a lighter object than a heavier one. Lightweighting has become the latest trend in automotive due to its implications in improving fuel economy, carbon neutrality and high performance. In a bid to comply with the increasingly stricter environment regulations automakers are already resorting to lightweighting and aluminium directly or indirectly will provide much of this savings. The metal once used sparingly as castings and extrusions in various auto parts and engines is now finding application in Body-in-White and closures. Both conventional vehicles as well as electric vehicles can enjoy the benefits through lightweighting without compromising on safety standards. This has led to a surge in demand for aluminium and also boosted aluminium production globally in last decade.
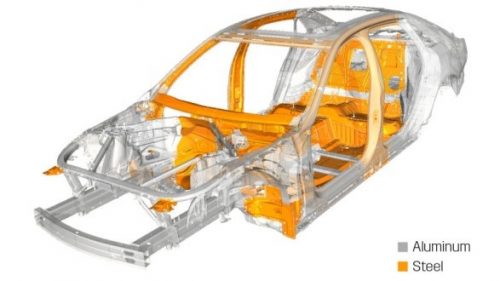
Aluminium is easily available, cheaper than other composites, the technology is tried, tested and offers seamless recycling benefits. Aluminium alloys with enhanced strength offer great potential for increasing vehicle efficiency due to their versatility, anti-corrosive nature, weight to strength ratio and infinite recyclability that is in the line of circular economy standards. At the end of a car’s life, more than 90 per cent of its aluminium content can be recycled into new car components or other products using only five per cent of the energy used in production of primary metals.
CAFÉ Standards
The Corporate Average Fuel Economy (CAFE) standards are regulations first introduced in the United States in 1975, to improve the average fuel economy of cars and light trucks produced for sale in the United States. CO2 emission standards have undergone stringent changes in recent times with the growth in automobile sale. The new revised CO2 standards base CO2 targets on a footprint-based approach than a mass-based approach which allows more lightweighting opportunities and opens up the door for more aluminium applications. Since the use of rolled aluminium sheet in Body-in-White applications can dramatically reduce the overall weight of a car, the consumption of rolled automotive sheets is bound to see a jump in future.
North America has been working strategically towards material substitution since 2014 and the EU policymakers are seizing this opportunity to realise its potential. North America’s footprint based approach for CO2 standards has dramatically increased the region’s investment in lightweighting technologies and the innovative use of aluminium in cars.
Aluminium content in vehicles:
According to IHS Markit’s Global light vehicle production summery, about 95 million vehicles were produced in 2017, and it will cross the 100-million units per year milestone by 2019. A Ducker Worldwide study that was commissioned by European Aluminium in 2016 determined that aluminium content of cars produced in Europe stood at 150kg, which will increase by up to 30% over next decade. This increase will be driven by rolled and extruded products.
Another Ducker Worldwide study commissioned the Aluminum Association of North America finds that the total aluminium content is expected to grow to 256.28 kg per vehicle by 2018, up from 180kg in 2015. By 2020, the total aluminium content for North American lightweight vehicles will increase to nearly 4.08 million tonnes, averaging 211kg by 2020.
The report also says aluminium vehicle parts will more than double in this review period. The average passenger car will contain 164kg of aluminium and the average light truck will contain 237kg of aluminium by 2020. Under this scenarios, aluminium will contribute more than 50% of the total mass reduction ranging from 270 pounds (7% MR) to as little as 170 pounds (4.5% MR) by 2028 and aluminium content will range from 494 pounds per vehicle to 565 pounds per vehicle.
Aluminium Solutions
Under this trend, all major automakers are shifting towards aluminium for lightweighting. Special alloys and tempers have been developed by the aluminium producers and are already in use by the auto OEMs and part makers that provides the properties needed to meet the specific quality requirements of the various parts. Auto part makers and OEMs demand higher quality aluminium alloys from producers for making casting, forging, extrusions and rolled products. Companies like STAS that provides material solutions for aluminium smelters have been regularly helping major aluminium makers. STAS manufactures and supplies various equipment to improve productivity and the quality of molten aluminium. Our technologies offer benefits throughout the entire spectrum of aluminium producers, ranging from primary smelters to secondary smelters and rolling mills and aluminium extruders as well. STAS equipment removes hydrogen, alkalis and inclusions during metal treatment, which are considered undesirable in metal processing and ensures improved quality of finished metal or alloys.
For instance, STAS’ ACD / Aluminum Compact Degasser is an in-line degassing equipment that treats aluminium while it is being transferred between the furnace and the pouring well, during primary/alloy ingot productions. With over 250 units sold, the equipment ensures there is no loss of metal during alloy changes, omitting the need to recast aluminium in a casthouse.
Automotive Applications
Cast products make up more than half of the aluminium used in cars. Aluminium forged products are used by automakers due to their high strength, reliability, and economic viability. Extruded aluminium is used as external webs or brackets.
Rolled products remain the second largest fraction of aluminium in automobile applications. However, despite its dominance, the share of aluminium castings in the total automotive aluminium consumption has decreased by 8 percentage points in the last 4 years. The share of rolled products has grown significantly due to the increased penetration rate for body closures and body structures. The change is more prevalent in C, D, and E-Segment vehicles. Electric Vehicles remain one of the key demand drivers for aluminium because of its demand for lightweighting which offers longer range and better performance.
Once doubted as a gamble, Ford’s F-150 all-aluminium pickup truck went on to become the best-selling trucks of the U.S. The company used 6xxx series aluminium alloy for its F-series vehicles. Since the first model, Ford has revamped F-150 several times. In the latest one, the company has been able to reduce the weight by some 317 kg by adding 490 kg of aluminium – or roughly about 25% of the vehicle’s total weight.
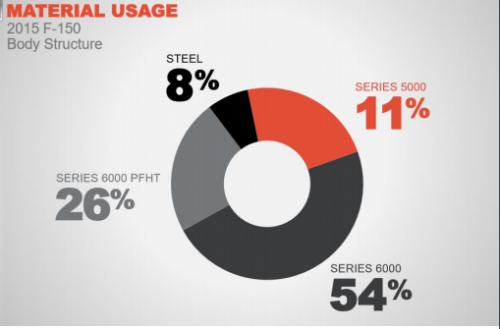
The shift towards lighter vehicles and a footprint based emission standard is opening up huge business potential for aluminium smelters and product suppliers. This important material shift in the automotive sector is driving the demand for aluminium and also for the equipment and technology suppliers who are contributing towards quality and process improvement in aluminium producers all through the value chain.